Généralité sur la méthode TDPC
Est une méthode qui fait partie de l’ensemble des outilles de L’OPS
Définition :
La méthode TDPC est un outil de classification des équipements selon quatre critères. T : temps d’intervention D : degré d’influence P : probabilité de panne C : criticité de la panne. Chaque critère il se compose en plusieurs coefficients ; le tableau suivant il résume tous les coefficients ?
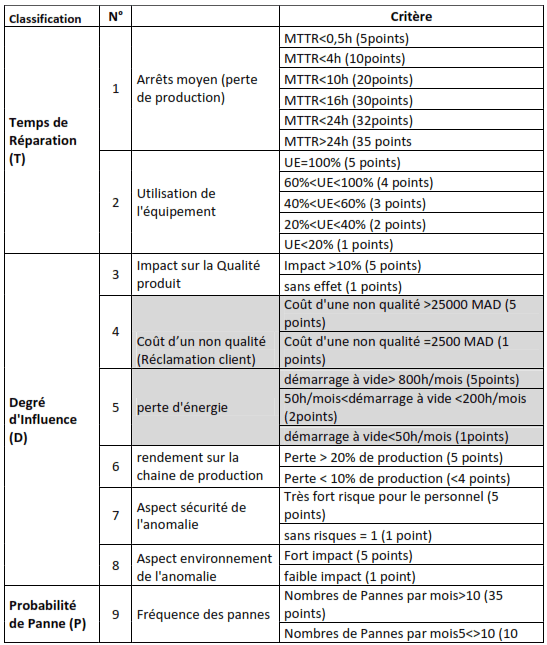
Cette démarche TDPC et valable dans des déférents contextes. C’est-à-dire selon l’objectif derrière, pour cela on est décidé de changer plusieurs coefficients afin de contribuer le coût de maintenance dans l’analyse. Parmi les critères modifiés celui de coût de non qualité remplacer par le coût de maintenance par ans.
Explication des déférents coefficients :
Première critère : temps de réparation
Il se compose de deux coefficients
1. Arrêts moyen (perte de production) :
On se basera sur les MTTR de chaque engin pour calculer la moyenne des MTTR pour chacune des flottes. Ce coefficient il mesure la maintenabilité des engins
2. Utilisation de l’équipement :
Remarque : on calcule toujours par la moyenne justement pour les flottes qui contient es engins ou machins identique. Pour le reste on distingue les équipements l’un de l’autre.
Deuxième critère : degré d’influence
Il résume l’effet sur la sécurité du personnel, l’environnement et les coûts. Il s’évaluera a partir de six coefficients suivants :
1. Impact sur la qualité du produit
Représente l’impacte de la défaillance sur la qualité du phosphate, dans notre cas les équipements étudiés n’ont aucun impact sur la qualité. Ainsi le coefficient sera prise égal à 1 pour tous les équipements.
2. Le coût de non qualité
Remplacé par le coût de maintenance, puisque la qualité de phosphate ne dépende pas des équipements pilot de production. Obligatoirement le coût de non qualité ne sera pas influencer par ces dernières. C’est la raison pour laquelle on a remplacé se facteur par le coût de maintenance, pour converger l’analyse vers l’objectif (analyse de coût de maintenance).
3. Pertes d’énergie
Egalement on a remplacé ce facteur par celui de la flexibilité des équipements, qui reflète la simplicité de manipulation. Ce facteur est simple à contrôler via la vitesse de déplacement. Souvent ces pertes sont dues au déplacement à vide.
4. Rendement sur la chaine de production
Se facteur il est calculer à partir des HM réalisé durant toute l’année 2017 que diviser par les HM prévus.
5. Aspect sécurité de l’anomalie
En générale les anomalies ils ont une influence soit en temps réel ou durant la réparation.
6. Aspect environnement de l’anomalie
L’OCP et engagé dans des accordes qui exige le respect de l’environnement. Pour nous les anomalies qui impacte plus l’environnement ce sont les fuites d’huile hydraulique et de gasoil, Ils apparaissent plus souvent sur les engins qui se fonctionnent à l’aide de l’énergie hydraulique comme les pelles hydraulique et les bulldozers D11.
Troisième critère : la probabilité de tomber en panne
Ce critère il se caractérise par la fréquence mensuelle des pannes. Il renvoi à la fiabilité des équipements. Un équipement considéré comme critique, si le nombre des pannes dépasse 5 pannes par mois.
Dernière critère : la criticité de l’équipement
C’est l’indice le plus significatif de cette étude. On notera cet indice en fonctionne des arrêtes de production ; c’est-à-dire comment l’équipement affect la chaîne de production.